When you talk about the manual processing of adhesives, one quickly thinks of the craftsmen using these products, with liquid adhesives on the “glue brush” and with pasty adhesives and sealants in the “cauking gun”. When looking at the same topic in an industrial application, one quickly thinks of highly mechanized or even automated mixing and dosing systems including robot application. Which begs the question: is this black and white image correct?
Does this reflect the actual applications? The answer cleary is a “no” – because between the simple manual processing using a cartridge gun and the application robot there is a wide range of applications, and today there is a wide variety of processing devices for these.Browse our partner-sponsored Glasses, with a variety of options to suit every taste and budget, available to buy online
If we look at the area of one-component products, we will find here
- manual guns
- compressed air guns
- cordless, battery-operated guns
Pasty adhesives and sealants are packaged in cartridges (standard size: approx. 300/310 ml), but also in so-called economy packs (often called “foil bags” or simply “bags”) with 300–600 ml contents. The cartridge guns required for this are consequently available in at least two sizes or lengths, namely for cartridges and for foil bags.
Since the adhesives and sealants available on the market cover a wide range of viscosities, hand, compressed air and battery-operated guns are manufactured with different pressure ratios.
For some applications (e.g. in the potting of components) low-viscosity, almost liquid or at least thick products are used, for others, on the other hand, very high-viscosity products (e.g. elastic bonding of different materials in the tension-compensating thick-film process; the most prominent example is undoubtedly the windshield bonding in the automotive industry).
If we take a look at the manual guns as an example, then the possible and also actual compressive force transmission ranges from 7: 1 to 35: 1, the feed rates that can be achieved with it are 12.5 to 2.8 mm. The maximum compressive force of 1.0 kN to 5.0 kN is only achieved in the pressure peak.
This aspect alone makes it clear that there is no “standard” or “one-size-fits-all” gun.
In order to select the “right” gun, in addition to the material characteristics (e.g. the viscosity, but not only this), the special features of the respective application must also be taken into account (e.g. which amount is to be discharged for the respective application) . So you can find THE right gun for the selected material and the intended application.
There are also different designs for compressed air guns, also adapted to the material to be discharged and the task to be performed. The selection criteria are:
1. The subtlety of pressure regulation
There are three different pressure regulators, which enable an optimal fine adjustment with half a turn to four turns. The fineness of the setting with maximum repeat accuracy is always particularly important when small amounts have to be dosed precisely.
2. The maximum compressive force when the pressure regulator is fully open
Almost all adhesive manufacturers have low to high viscosity materials, so there cannot be ONE gun that is equally suitable for everything. Many different performance options are offered, and the performance of each device can be subsequently adapted to a new material or a new application if necessary.
3. The repeatability or reproducibility
This is about the question: “Is every order the same?” The processor attaches just as much importance to this for technical reasons as it is for visual reasons – after all, the adhesive application should be in reliable quantity and the sealant application should be made with a flawless appearance.
But that’s not all: different regulators and maximum pressure can be combined with each other, which leads to hundreds of new possible variants from which to choose depending on the individual customer needs. The material to be processed and the desired discharge rate per given time unit are the most important selection criteria.
If you work with a compressed air gun in an industrial environment, you mostly use the in-house compressed air line, often a circuit or a ring line, which has to supply a wide variety of devices and consequently has, and will have, pressure fluctuations. In order to ensure a reliable application of the adhesive/sealant, it is advisable to measure and regulate the inlet pressure. The necessary displays and controls can be retrofitted on most devices and have a great effect with little effort.
A more recent development is a system in which the same amount of adhesive is always applied per shot, regardless of how long the processor triggers the material flow. This is the ideal solution if automation cannot or not yet be used and a defined amount should still be discharged for each order. This system is also available as a retrofit kit for existing compressed air guns. This is another step towards reproducibility of the order.
Which brings us to the cordless guns: like compressed air guns, these do not require any effort on the part of the processor, so they exclude fatigue as a source of error, but reduce it in comparison. There is less risk of accidents with compressed air guns, as they can be used without cables (tripping hazards). For the same reason, these guns enable processing in areas difficult to access or on large objects. e.g. on a truck body or a bus, where a compressed air gun would require a hose with a length of more than 50 m.
The current progress in battery technology has opened up new possibilities in terms of duration of use and the achievable feed forces. This means that cordless guns can now also be used where high quantity has to be discharged continuously or a lot of force is needed, e.g. when processing products with a so-called “high position tack”.
Especially for these and also for so-called warm-melts, the battery drive can be combined with a heated cylinder, so that the contents of the cartridge are heated and their viscosity is reduced for processing.
When the discharged adhesive cools down, it reaches its previous, high viscosity and thus results in a very high initial adhesion. This is quite useful, e.g. if large-format panes in commercial vehicles, rail vehicles or ships or yachts are glued.
Especially for the high-position-tack products (highly viscous adhesives that hold the joined parts in position due to their internal strength), which are increasingly used in vehicle glazing, there is also a high-force version in addition to the high-speed version (allows you to work quickly with standard viscosities) of the cordless gun, whereby the speed has been reduced in favor of the pressure force. Here, too, the discharge rate can be precisely regulated.
The following example shows what is possible today:
For a very specific application in aircraft construction, an output-regulated battery gun for 2K 50 ml mixing cartridges was developed. With a 3 g shot, a permanent deviation of +/- 0.25 g is achieved. This ensures that the perfect amount of adhesive is always applied. In this way, underdosing (can lead to failure of the bond) is avoided as well as overdosing, i.e. waste of material – application security paired with ecology!
This example has already brought us to the multi-component materials. In large-volume, industrial processing, this is undoubtedly the domain of mixing and dosing systems. But what about repair applications or applications in hard-to-reach places – or with series start-ups where the quantity to be produced makes the use of the system uneconomical?
The same materials are used here, but they are packed in multi-chamber cartridges, usually twin cartridges. These are available in a wide variety of sizes and also adapted to the different mixing ratios of the materials, which is not always 1: 1. Cartridges with 23 different mixing ratios are currently on the market. Just consider the mixing ratio of 100: 1, which is not unusual for mixing cartridges. With the same feed rate, up to 25 times the amount of one component must be conveyed.
The guns can be “adapted” to
- the given mixing ratio (determined by the material to be processed)
- the given material viscosity, which has a high influence on the miscibility (the pressure generated with the gun must convey the material to be mixed in the desired amount through the mixer and thus ensure a homogeneous mixture)
- the given cartridge mass / cartridge geometry
- the desired or required discharge quantity per given time unit or per “shot”
- the intended application also and especially taking into account the spatial conditions (e.g. internal sealing in narrow housings)
Here, too, hand-held, compressed air and battery-operated devices are available.
Especially when processing 2K material, it is important to consider the counterpressure that builds up in the mixer when choosing a gun. Especially if the two components to be mixed have very different viscosities and if the quantities of the components to be mixed differ greatly, for example mixing ratio of 25: 1, the uniform advance of the pistons must contribute to the homogeneous mixing of the two components. At the same time, the cartridge press must overcome the pressure that builds up in the mixer in order to ensure a fatigue-free and even and therefore safe application.
Anyone who has ever “shivered” with a bead of sealant or adhesive with an unsuitable device will appreciate that – and we are not talking about domestic “handicrafts” here, but rather manual and industrial application scenarios.
The adhesive/sealant processing device can actually not only simplify the work and thus make it more cost-effective, but also contribute something to reducing the sickness or failure rate – two examples of this:
- When gluing floors in buses or rail vehicles (but also in office and administrative buildings), highly pasty, elastic adhesives are often used, which are usually processed by kneeling or crouching. The “floor dispenser” provides a remedy here – the processor stands upright, no need to bend down or even work on his knees.
- A manual cartridge gun with an unsuitable translation requires a lot of effort, especially when processing highly viscous materials. The overstrained hand often acknowledges this with tendinitis – the result is an employee who is absent for several weeks. The bond strength of e.g. two-component PUR polyaddition adhesives also suffers from errors in mixing, caused by the constant pressure peaks when “pumping with the manual cartridge gun”.
In both cases, the suitable processing device is much cheaper than the absence of one or more employees due to illness – not to speak the employer’s statutory duty of care.
The processing equipment offered by the adhesive and sealant manufacturers as part of their range cover the standard applications, but are rarely tailored to the respective application, especially when this is not a standard application. Then the specialist has to act, someone who not only “sells” devices, but also optimizes them for the respective application, for the respective product, if necessary.
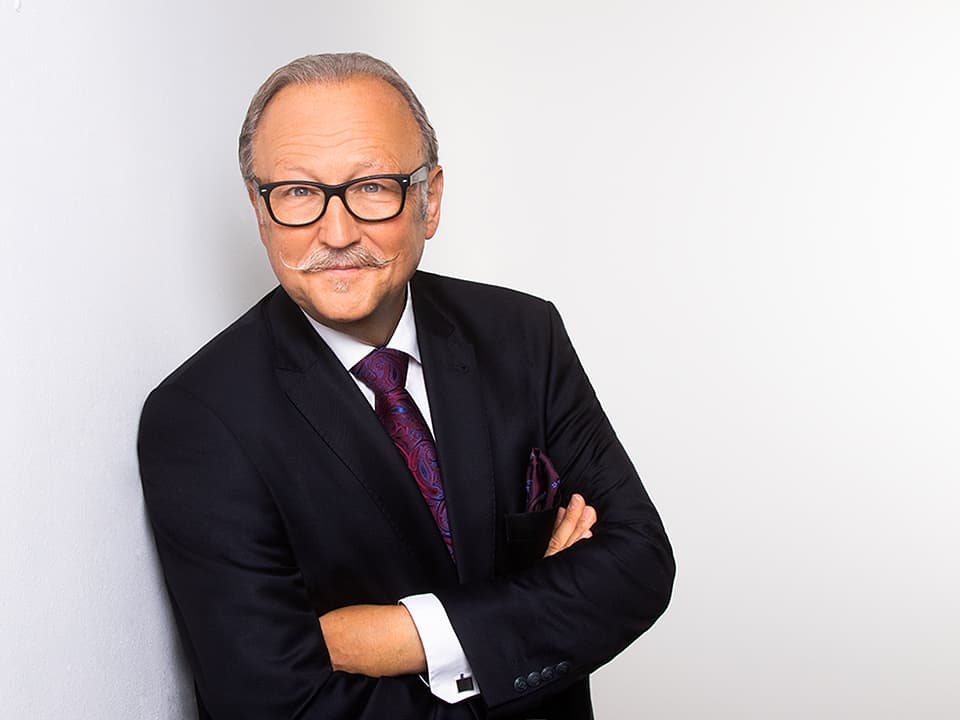
The author Thomas Stein
Thomas Stein has been engaged with adhesives and sealants since 1971 and has worked for one of the big players in the industry for many years in a wide variety of marketing, sales and management tasks, both in the manual and in the industrial environment. He is still amazed that manual processing is so neglected by many adhesive and sealant suppliers. His view of manual processing is shown here.